Valves from Schubert & Salzer Control Systems are used in the manufacture of paper and its basic material, wood pulp.
Wood pulp production
Whether it is in the cooking of the wood chips needed for the production or in the washing, bleaching and drying of the wood pulp resulting from it, wood pulp production presents ideal conditions for using the sliding gate valves and ball sector valves from Schubert & Salzer.
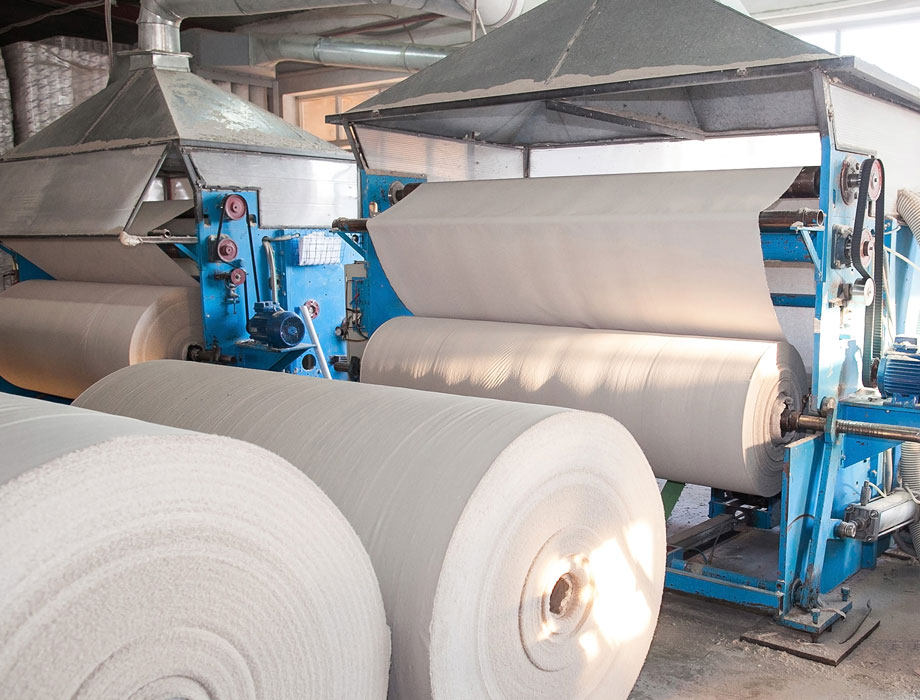
Sliding gate valves are particularly suitable for steam processes. The generation of steam and its use are of special importance in the wood pulp production process. Here, the wood chips are packed tightly in the cooker with the aid of steam and cooked under pressure and high temperatures. Sliding gate valves are used in drying the so-called “pulp”, in which the valves regulate the supply of hot air for the drying process. Similarly, they are used to extract water from the so-called black liquor in the evaporation plant with the aid of steam.
At the heart of this valve are two slotted discs sliding against each other and forming a seal. The pressure difference forces the moving gate against the stationary disc. Thus, the sliding disc valve seals itself without the need for a metallic seat. Users appreciate the much lower energy consumption, due to the short stroke, and the optimal flow control. With their compact construction, sliding gate valves are also very maintenance-friendly. An overview of all features of this valve series can be found by clicking here.
Ball sector valves can be used for nearly all shut-off and control tasks, in particular where media are soiled, abrasive or pasty. They are particularly suitable in wood pulp production, for instance in brown stock screening and washing and in the regulation of fresh water and effluent processing. With ball sectors specially machined out, they are self-cleaning and can be actuated very precisely with pneumatic and electrical actuators and controllers. Click here for other properties of ball sector valves.
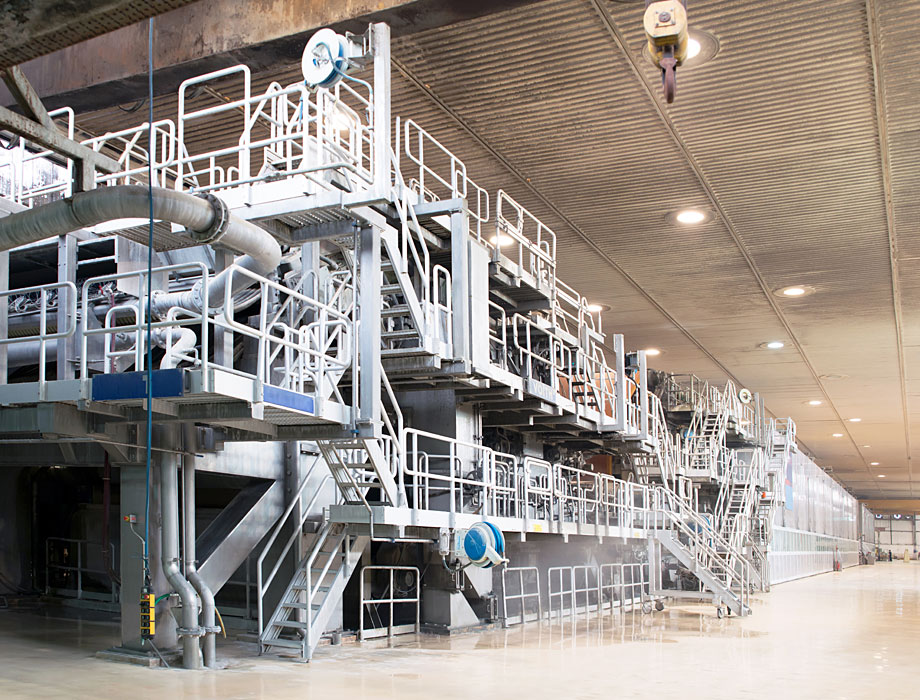
Paper production
In the next step, paper is produced from the wood pulp. This also presents a wide range of opportunities for using the sliding gate valves and ball sector valves from Schubert & Salzer Control Systems.
The paper and wood pulp industries are extremely water-intensive. In the manufacturing of paper, water is needed for the suspension and transportation of the pulp as well as in ancillary (sealing water, cooling water) and cleaning applications. With their elliptical opening areas, ball sector valves are used here as, on the one hand, they do not dehydrate the pulp in the control process and, on the other hand, they are extremely resistant to abrasive media. The control of pasty media is outstanding due to the special opening geometry of the ball sector valves. Properties of ball sector valves can be found here in detail.
When it comes to controlling the grammage in the production of papers with weights ranging from about 20 g/m² up to cardboards up to several 100 g/ m², using a ball sector valve offers unique advantages for high precision process control. The combination of a highly accurate servo actuator with 8192 steps and a zero-play ball sector valve can offer a precision valve unit even for high flow rates. The decisive factor in achieving high precision has been in providing an absolute angle transducer which detects the actual position of the valve unit in real time and feeds it back to the controller as an output value. It is possible, therefore, to set volumetric flow rates, as, for example, in regulating the quantity of pulp, with the utmost precision. Further information on this can be found at application report - paper manufacturer Gebr. Grünewald.
Sliding gate valves are best used in the paper production process where steam is involved whose supply must be regulated precisely. This is the case, for instance, in the so-called dry and press section where the pulp, after breaking down and mixing with fillers and auxiliary material is guided in the paper machine over steam heated cylinders where they are pressed indirectly and finally dried.