We don’t have to look far in our daily lives to find plastics or rubber – from rigid plastics in a computer screen or in a pen, right through to rubber in balls or vehicle tyres. The manufacturing process for such products is very involved and demanding. A wide variety of products can be manufactured from the raw materials only at high temperatures and pressures.
Already in the early processes of obtaining petroleum in the refinery and in the cracking that follows, Schubert & Salzer Control Systems‘ valves, in particular the sliding gate valves, are used to control oxygen in the furnaces of the fractionating columns.
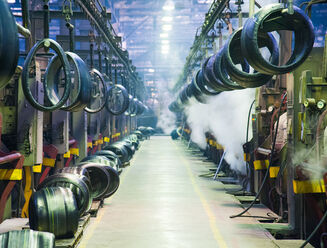
Valves from Schubert & Salzer Control Systems are used everywhere in the downstream manufacturing and processing stages where moulds are heated by steam or hot water, heat treatment and melting processes take place and plastics are mixed or cooled or themselves are being controlled in liquid form.
One example of an application is the sheathing of cable, in which sliding gate valves control steam and water to harden and cool the sheathing materials. Sliding gate valves are used also in the production of CDs and LPs, where the temperature in the presses is controlled by steam. Other applications can be found in the manufacture of plastic pipes, such as in the cooling and calibrating sections, in the blow moulding of hollow plastic bodies such as fuel and chemical tanks, barrels and rainwater butts, and in the foaming of EPS and PPS products.
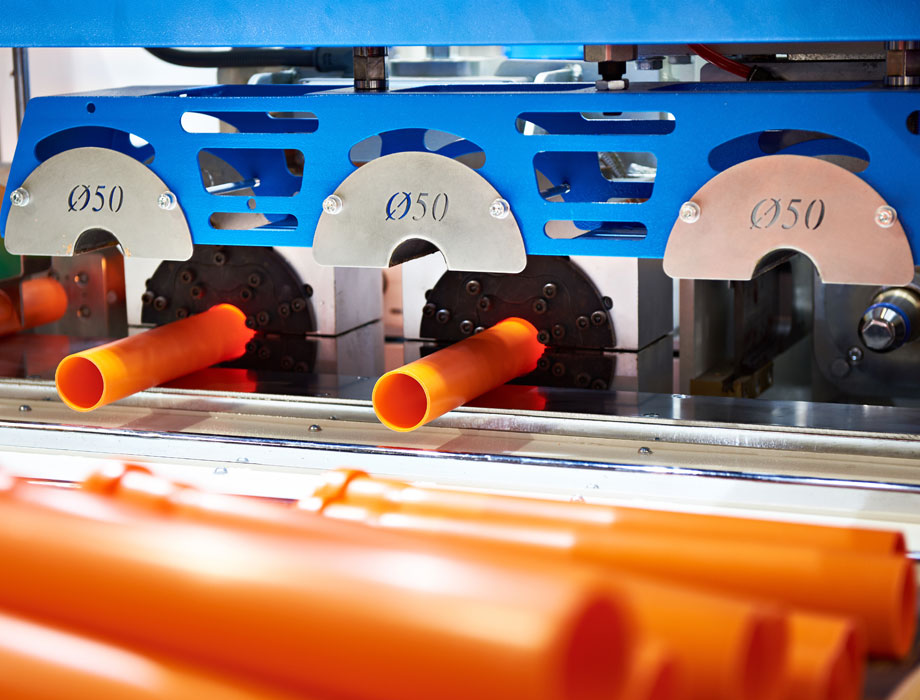
A process at the heart of rubber products is vulcanising. Here, the natural rubber/sulphur mass is made resistant to environmental and chemical effects and mechanical stress by subjecting it to high temperatures and severe pressure over a specific time period. This process is needed to produce an elastic material from the original rubber for further processing.
This important and elaborate production process places great demands on the valves used in the plant: restricted installation dimensions, outstanding positioning ratio, fast reaction times, reduced energy consumption and simple maintenance.
Two particular types of valve from Schubert & Salzer Control Systems have proven their worth in this area:
The stainless-steel version of the Type 7010 angle seat valve excels itself as a stop valve, due to its high Kvs values coupled with its extremely compact construction, many possible connections and very easy maintenance. The high temperature versions guarantee a high quality seal and long service life even in applications up to 220° C. Their high resistance to wear, even after several million switching operations, is a particular advantage of the Type 7010 angle seat valve. This is particularly important under the critical conditions in vulcanisation, with deposits and corrosion in the pipeline. Schubert & Salzer’s seat valves have been shown to run with no problems for 2-3 years without leaking – even under the critical conditions encountered in vulcanisation.
Above all, the sliding gate valve from Schubert & Salzer Control Systems has shown its worth as a control valve. This valve series controls and switches liquid, vapour and gaseous media precisely, rapidly and economically.
The following characteristics of sliding gate valves have proven to be particularly beneficial in the vulcanisation plants:
• long service lives
• optimal adaptation to each operational requirement in the plant with an
• appropriate Kvs value and characteristics
• prolongation of the valve service life due to having optimal Kvs coefficient and characteristics
• high quality of control by the sliding gate valves enables the press cycles to be shortened
• simple and quick maintenance of the valves due to easy exchange of worn parts
For more detailed information please download our brochure: Schubert & Salzer – Your Partner in Tire Manufacturing