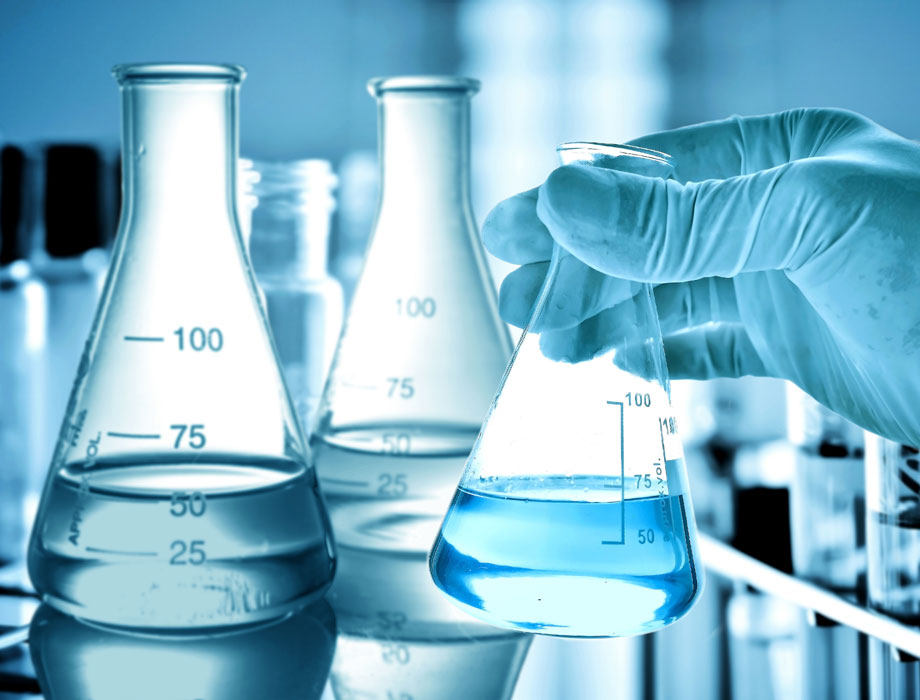
Inorganic and organic chemicals are omnipresent and an indispensable part of daily life. The manufacturing processes in which liquids and gases as well as powders and paste-like media are shut off and controlled are diverse and complex. The valves required for this must meet the highest standards of control accuracy, reliability and durability. Safety in explosion-proof applications as well as high internal and external leak-tightness of the valves are basic requirements for operation in chemical plants.
Sliding gate and ball sector valves from Schubert & Salzer are used in the manufacture of basic chemicals such as ethylene, sulphuric acid and caustic soda as well as in further processing into chemical intermediate and end products such as plastics, paints and varnishes as well as fertilisers.
Valves for heating and cooling processes
Steam, thermal oil and cooling water are important auxiliary media in the thermal processes for the manufacture of chemical products. Sliding gate valves impress in these applications due to their control accuracy, high reliability and long service life with minimal energy consumption. They cover a wide temperature range, have low heat losses due to their compact size and can be insulated extremely well. The energy-efficiency of thermal processes can be increased as a result.
Typical applications for sliding gate valves in thermal processes are, for example, mixing vessels for the manufacture of resins, powders and phenols; evaporation and drying systems, e.g. for the manufacture of silicic acids and titanium dioxide; as well as distillation columns for the manufacture of aromatic hydrocarbons.
Valves for extreme conditions
Aggressive media, high pressures and temperatures are the speciality of sliding gate valves. Made of alloy, they are a crucial component in acid dilution, for example in the manufacture of ultra-pure sulphuric acid. They compensate precisely for product fluctuation widths of up to 100% with maximum control accuracy and dynamics. Other applications include the control of nitric acid, ammonia, vinyl acetate or trichlorosilane in polysilicon production. Due to their short stroke and the very low moving masses, sliding gate valves are ideally suited for applications with high switching capacities and for the generation of pressure pulses, such as in the cleaning of filter elements in hot gas filters or in the manufacture of carbon black.
In the case of paste-like and particulate media, ball sector valves often solve problems when used as stop or control valves. Due to the specially shaped ball sectors, the valves achieve a very high control accuracy and a large volume spread, as well as being extremely wear-resistant even with highly abrasive media. Ball sector valves are used, for example, in the dosing of paint suspensions with a solid content, in lubricant production, for the control of limewash as a neutralizing or flocculating aid, as well as in the manufacture of stearic acid.
Small flow rates and high pressures can be precisely regulated or securely shut off using low flow valves. They are used wherever small volumes of gases or liquids, measured in only a few liters per hour, need to be metered for reaction processes.
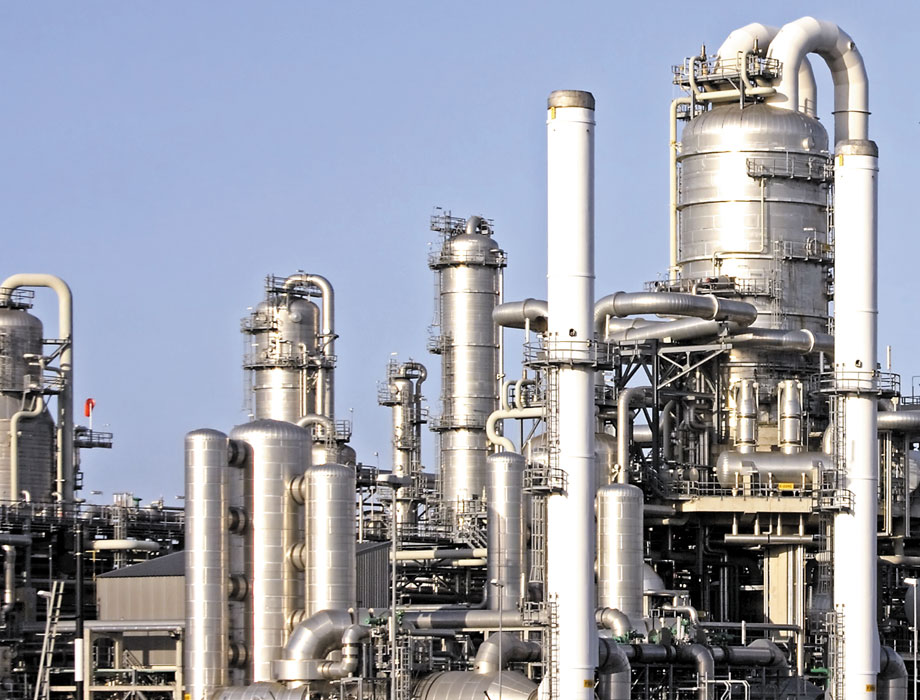
Valves for areas with potentially explosive atmosphere
Chemical processes often require the handling of flammable gases, vapours and dusts. These production plants are therefore subject to strict requirements with regard to explosion protection. Stop and control valves from Schubert & Salzer are approved and suitable for use in these areas in accordance with ATEX 2014/34/EU. For systems with explosion protection requirements based on U.S. and Canadian standards, valves from Schubert & Salzer are also available with FM certification (Factory Mutual Approvals) for Class I, Division 1 or Zone 0 intrinsic safety circuits or for Class I Division 2 non-incendive circuits.
Valves with a high leak-tightness
Reliable internal and external leak-tightness is an important prerequisite for the safe use of On-Off and control valves in chemical plants. All sliding gate valves and ball sector valves as well as special seat valves comply with the TA-Luft (Technical Instructions on Air Quality Control) requirement with EN ISO 15848-1.
Sliding gate valves are suitable for this purpose due to their special design principle. Leakage rates of less than 0.0001% of the Kvs value are achieved. This corresponds to leakage class IV according to IEC 60534-4. The short stroke of the sliding gate valves of only 6-9 mm leads to a long service life of the spindle seal and spindle, even with high switching frequencies and continuous control operation. As a result, the external leak-tightness is maintained.
Valves with metal bellows are chosen for the handling of hazardous media. They seal to the outside with 100% reliability.
Resource-saving valves
As an energy-intensive industry, the chemical industry has a special responsibility to make production processes sustainable and resource-saving.
Sliding gate valves from Schubert & Salzer can help to achieve this goal. Due to their special design principle, they require only minimal actuating forces. For example, in an application for the manufacture of EVOH resins, such as those used in multi-layer food packaging, switching to sliding gate valves saved over 80% of the control air and rapidly reduced operating costs.
A sliding gate valve in the size DN 150 weighs just under 15 kg, while a globe valve often weighs 150 kg or more. This not only makes the installation, insulation, maintenance and repair of the valves much easier and more efficient, but also saves immense resources in the manufacture and transport of the sliding gate valves due to the significantly lower use of materials.
Selected references
Application examples for stop and control valves in the chemical industry:
- Manufacture of basic chemicals such as caustic soda, technical chlorine, sulphuric acid, hydrochloric acid, ethylene, etc.
- Manufacture of paints, varnishes and solvents
- Manufacture of polysilicon / control of H2, N2 and trichlorosilane
- Manufacture of hydroxypropyl methylcellulose (HPMC)
- Control of stearic acid
- Manufacture of synthetic resins (control of steam, cooling water, vacuum)
- Manufacture of fungicides and herbicides
- Control of catechins (muddy, crystallising)
- Manufacture of fine chemicals
- Manufacture of chemicals for the production of adhesives
- Manufacture of fertilisers
- Manufacture of carbon black (black) and titanium dioxide (white)
- Manufacture of special plastics, e.g. for car headlights and branded toy building blocks
- Manufacture of detergents
- Manufacture of synthetic rubber
- Manufacture of lubricants
- Manufacture of polystyrene for packaging material
- Control of vinyl acetate
- Manufacture of organic phosphorus for detergents